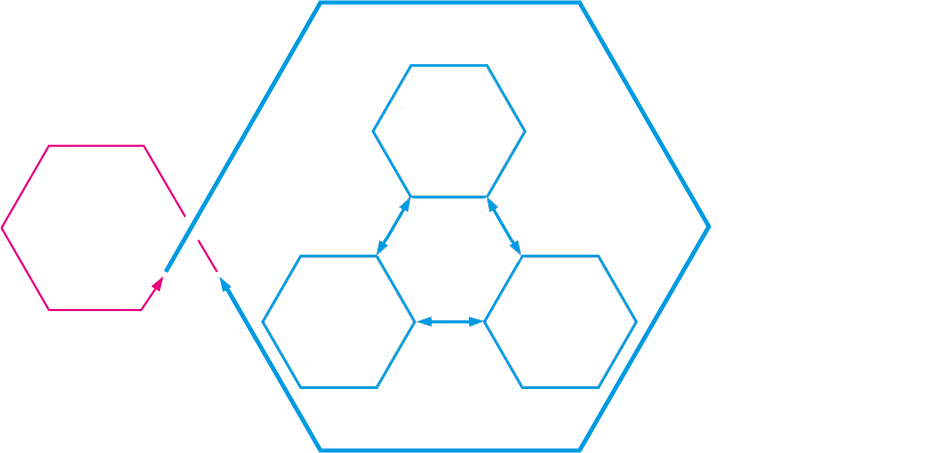
Our R&D and Engineering Departments’ mission is to develop new design effects, while maintaining the highest in quality and performance. Our engineers cooperate closely with our design team, gathering information from a variety of sources and analyzing it with an expert eye. We verify these data and test the effectiveness of each technology directly in our domestic facilities. All processes, from performance testing to mass production, are managed by our fully integrated organization.
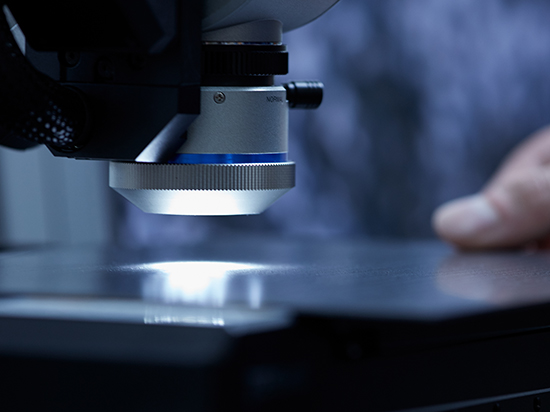
-
with a multi-faceted approach - Our researchers constantly pursue both pure research, i.e. the theoretical consideration of materials, pigments, and printing technologies, and also applied research, in which these theories are applied to develop real products. At the factory level, our engineers continuously research new ways to improve production efficiency while maintaining quality. In order to achieve superior quality and performance, we have assembled a team of experts in each field, who work together to further research.
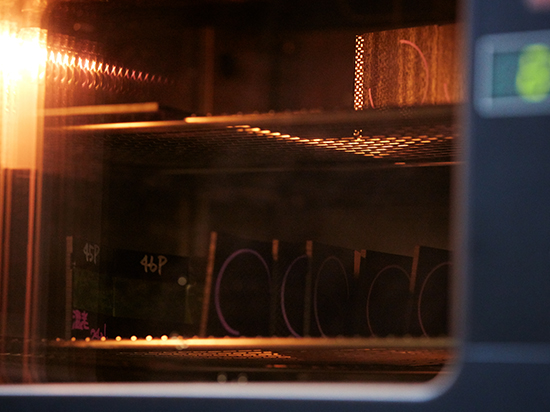
-
production with repeated testing - Our R&D team pursues long-term research and technology validation in parallel with sample development in collaboration with our design team. In order to meet the quality standards, set by the customer, the cycle of testing and improvement is repeated many times. At the same time, our engineers begin planning factory and equipment layout in order to reliably produce the product.
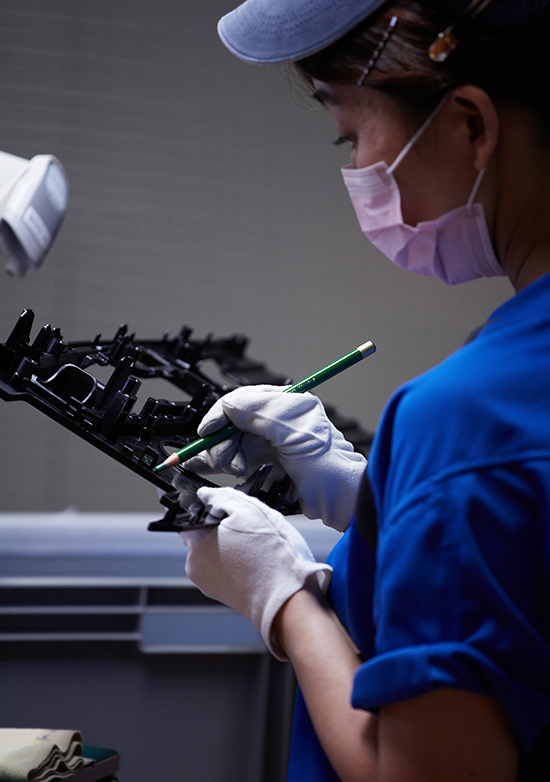
-
- Flexibly adapting to the fast pace of advances in materials science, engineering, and decoration technology, our research engineers are constantly on the lookout for new information to enable us to recommend new, reliable solutions. In addition to staying up to date with the latest regarding domestic and internationally available information about printing technologies, our R&D team develop new design effects by applying knowledge gained during tireless field work. This includes interactions with professionals from other industries, cooperation with educational institutions, and attending trade shows.
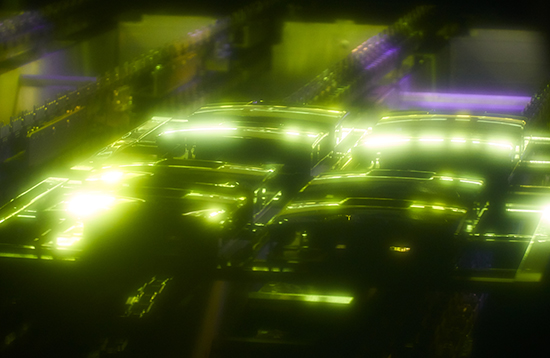
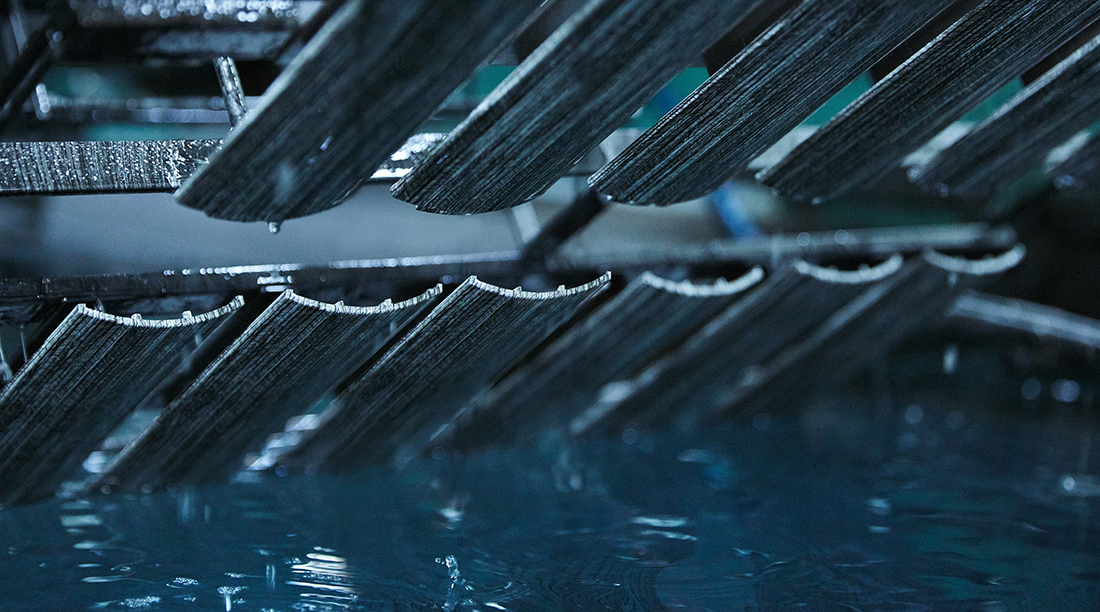
- The Hydrographic Printing Process
- Hydrographic printing involves floating a special printed film on water and then using water pressure to transfer the printed pattern onto a substrate material. The substrate is then dried and painted. One of the main strengths of hydrographic printing is the ability to print onto complex geometries and large substrates. Taica's Hydrographic Printing process can produce a variety of texture and design effects by changing the steps taken after hydrographic transfer.
- Superior Pattern Coverage
- One main benefit of hydrographic printing is its unparalleled pattern coverage. By utilizing the power of water pressure, it is possible to apply printed designs evenly onto even the most complex part geometries. Additionally, hydrographic printing can be used on parts up to 1 meter in length. Hydrographic printing makes it possible to customize the transfer conditions for each part in order to optimize product quality.
- Design Customization
- The final Hydrographic Printing decoration appearance is the result of the complex interplay between substrate, ink, and top coat layers. The ability to adjust each of these layers allows for a high degree of design customization. For example, combining opaque and transparent inks in a single pattern allows us to use the substrate color itself as a distinct design element. Using a metallic substrate, for example, produces extremely brilliant decorations. The gloss, color, and other attributes of the protective top coat can also be customized.
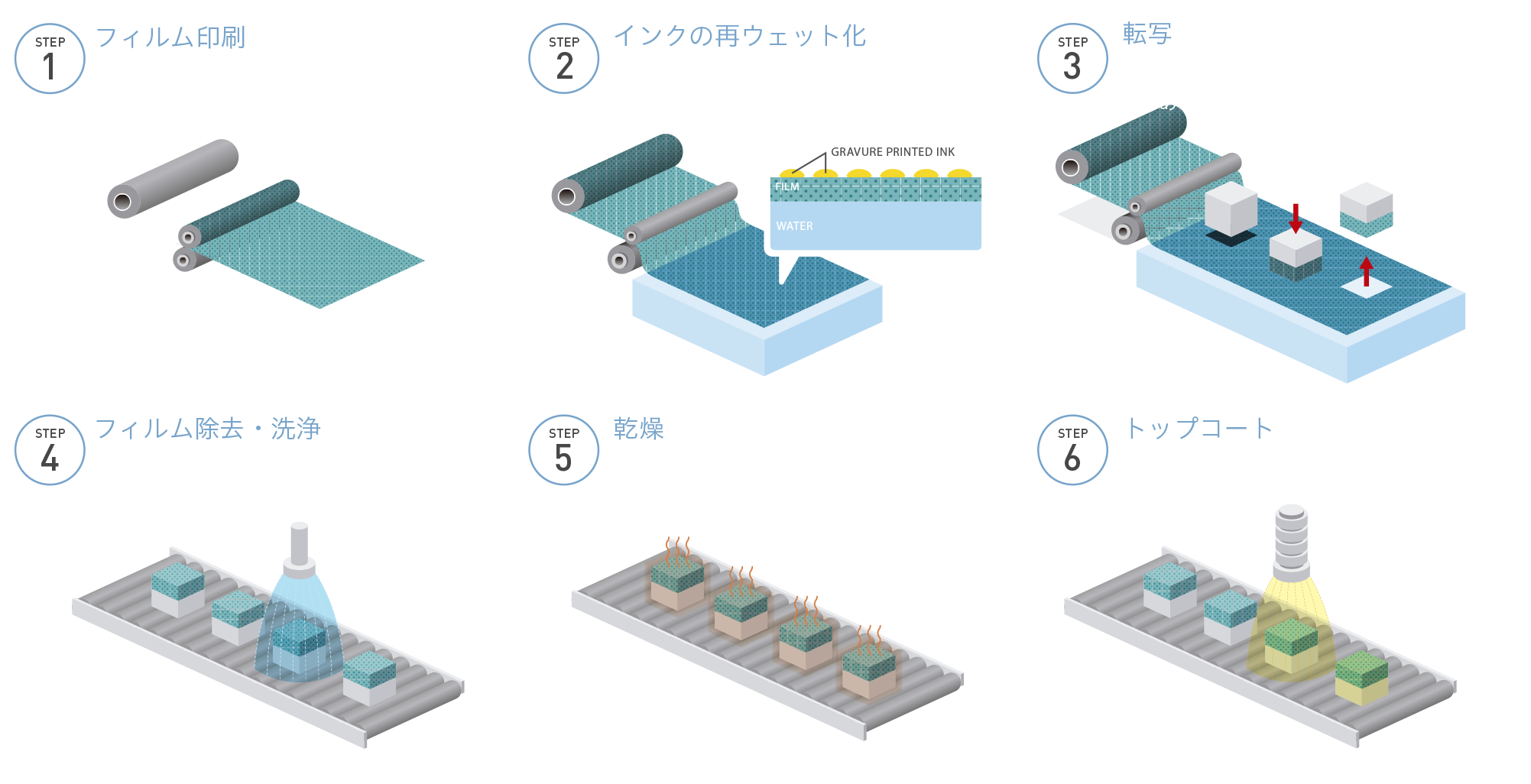
![]()
![]() |
![]()
![]() |
![]()
![]() |
![]()
![]() |
![]()
![]() |
![]()
![]() |
Material Expressions
Using our proprietary techniques, Taica continues to push the limits of decoration technology,
adding new value to a variety of familiar products.
- The world’s first hydrographic printing technology, CUBIC PRINTING has made countless achievements over the years. Adjusting the top coat paint produces full gloss, tinted clear, soft touch, and other effects.
- A high-definition version of CUBIC PRINTING that also makes exciting, new effects possible. S-CUBIC brings out the fine details in our patterns in a visually pleasing way. Also, adding sparkling pigments makes it possible to increase the personality and value of materials.
- An environmentally friendly, top coat-less technology featuring a smaller carbon footprint and reduced VOCs compared to standard CUBIC PRINTING. Unique effects, including matte-gloss and real haptics, make E-CUBIC decorations extremely realistic in both appearance and texture.
- H-CUBIC achieves brightness and three-dimensional effects approaching those of real metal using a special, proprietary film construction. This ground-breaking, Taica original technology pushes the limits of material expression, combining both reality and originality.